Basic Planning (Conceptual Design) in Factory Construction
Once the business concept is solidified, the next step is to move to the basic planning stage. During this stage, the overall approach to the factory is designed. In addition to the basic requirements outlined in the business concept, the factory’s concept, a list of relevant regulations, and internal company rules are used as the basis for specifying production volumes, product types, and other details. This information is then used to design process flows, layout diagrams, and floor plans. At the end of the basic planning stage, a design review is conducted with all stakeholders present to ensure that the created design documents meet the basic requirements.
Flow of Basic Planning (Conceptual Design)
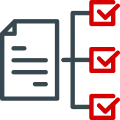
Organizing the Concept and Relevant Regulations
Confirm the concept and review the regulations.
Verify the consistency between the mid/long-term plan and the factory concept.
List relevant regulations and confirm specific requirements for each regulation.
List applicable internal standards and confirm specific requirements for each standard.
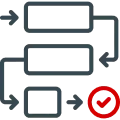
Confirming Conditions Related to Production
Specifically set the conditions related to production and create the process flow.
Clarify conditions related to production such as production volume, product types, production methods, operational plans, staffing plans, and logistics plans.
Regarding production methods (manufacturing processes), create a Process Flow Diagram (PFD) for API factories and a Material Flow Diagram (MFD) for formulation factories.
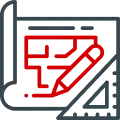
Confirming the Factory Layout
Based on the process flow, concretize the factory layout.
Based on the PFD or MFD, create a layout diagram of the production area.
Consider the flow of personnel and materials and the cleanliness zones, and create a functional relationship diagram indicating the correlation between production rooms and necessary areas in the factory such as changing rooms, preparation rooms, control rooms, machinery rooms, and hallways.
Roughly create a site plan for the factory that can maximize the potential of the intended factory site.
Create a site plan and building plans (floor plans, elevation plans, and section plans) that can simultaneously achieve the three planning aspects above.
Review the created proposals from the perspectives of cost and risk, and refine them.
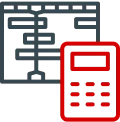
Estimating Construction Costs and Revising the Schedule
Estimate construction costs and the construction schedule and evaluate/review them.
Before moving to the detailed design, estimate the construction costs to determine whether it is feasible to proceed with the review. Calculate using methods such as estimating construction costs based on the unit area cost determined by the cleanliness zones in similar projects and the total floor area for each cleanliness zone. As for the construction schedule, verify more specific details and consider a schedule in units of 2-3 months.
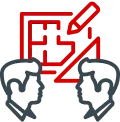
Design Review
Conduct design review and make final adjustments.
Gather stakeholders to review the design created in the basic planning stage from various perspectives.
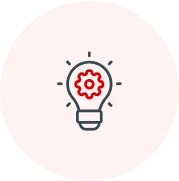
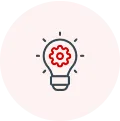
During the steps of basic planning (conceptual design), the overall framework for factory construction is designed. At this stage, it is crucial to organize the flow of people and materials, confirm basic functions, and ensure that the design complies with regulations and guidelines.
Key to Success
Project Team Composition ~ Specialized Skills and Overall Coordination ~
A factory encompasses a wide range of areas from production equipment to building facilities, and quality control to safety management. Therefore, it is necessary to advance the project by gathering the experience and knowledge of various experts. At the same time, it is essential to organize these experts into a project team and consciously aim for the overall optimization of the project, not just focusing on the circumstances of each expert. This also strongly tests the skills of the facilitator.
Sharing Members’ Awareness ~ Utilizing the User Requirement Summary (UR) ~
Factory construction is a significant investment, leading to the clash of opinions from stakeholders in different positions, resulting in many discussions. In the course of these discussions, it is crucial to document and share the core requirements (User Requirements: UR) to minimize discrepancies in understanding among team members.
Furthermore, in Pharmaceutical Factories…Awareness of GMP
GMP requirements need to be incorporated at the basic planning stage. It is desirable to thoroughly confirm these requirements at this stage to avoid having to redesign during the Design Qualification (DQ) stage.
-
Please refer to this for Qualification and Validation activities.
At CM Plus…
Supporting Client Meeting Management
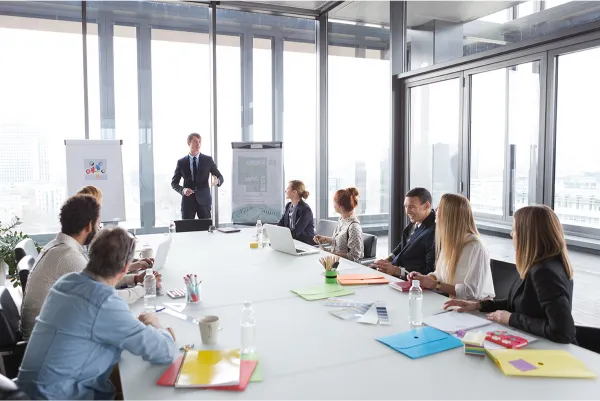
Experienced Project Managers (PMr) support clients in managing their meetings. By clearly presenting a schedule and a list of deliverables in advance, we progress basic planning according to the plan. CM Plus provides statements and advice from the position of a specialized third party, which can be utilized to coordinate opinions among internal stakeholders and drive the project forward.
Creation of User Requirement Summary (UR)
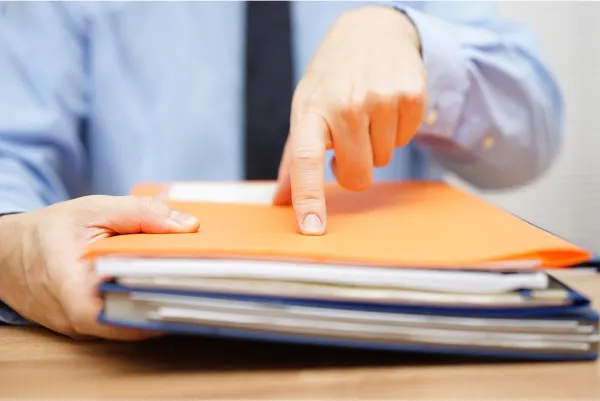
We create a document with an index structure tailored to the client’s factory and document the requirements. By consolidating the requirements into one summary document, not only documenting the design process in meeting minutes, but also providing a comprehensive view of the connection between the project requirements, assumptions, and the final design deliverables.
In Pharmaceutical Factories…GMP Compliance Assessment
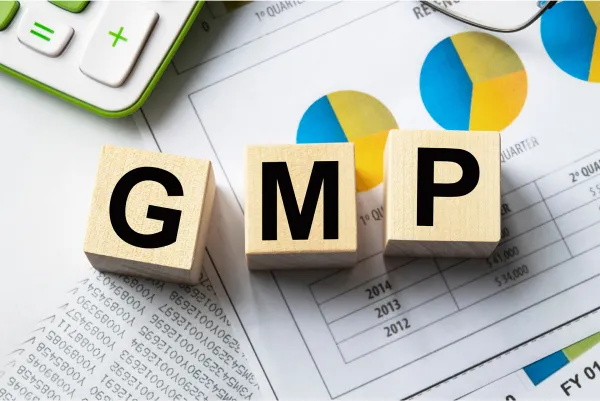
As part of the design review, we evaluate and document whether the basic requirements such as flow lines and cleanliness zones in the factory meet GMP standards. We use a unique assessment list based on the latest GMP requirements to make our judgments.
What is UR
UR stands for User Requirement (or User Requirements Brief) . In ISPE’s (International Society for Pharmaceutical Engineering) publications, it is defined as “requirements for facilities and equipment regarding the products to be manufactured, the production quantity (processing amount), and their conditions.” (C&Q).
What is URS
URS stands for User Requirement Specification. In various ISPE publications, it is defined in expressions such as:
- “A document that describes the requirements for the facility in which a product is manufactured, the necessary processing amount, and the environmental conditions for product manufacturing.” (TT2)
- “A description of the requirements for facilities/equipment regarding the products to be manufactured, production quantity (processing amount), and their conditions.” (C&Q Water and Steam)
In other words, URS is the user’s requirement (UR) expanded into the specifications necessary for the design, fabrication, and construction of the facility, system, or equipment. At CM Plus, we believe it is essential for the design personnel to utilize every means to understand the UR from the user, which can vary in various forms according to the user, and reflect it in the URS items.
See other phases
Related Contents
Useful Information
Please also refer to the articles on our information dissemination site, “GMP Platform.” Although the title contains “Pharmaceutical Factory Construction,” the content is applicable to the construction of factories in various industries, not limited to pharmaceutical factories.
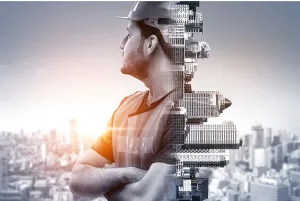
“How to Build a Pharmaceutical Plant”
Integrating know-how for the success of pharmaceutical factory construction projects. It provides detailed explanations and key points for each step, from overall project planning (= creating the project framework) to basic planning and basic design.
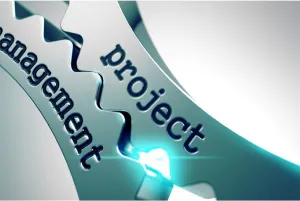
“Owner’s Project Management in Pharmaceutical Facility Construction 2nd Edition”
The fifth installment in the series on owner’s construction project management. What is basic planning (or conceptual design)?