Classification Name | Low Molecular Weight | Medium Molecular Weight | High Molecular Weight |
---|---|---|---|
Molecular Weight |
|
|
|
Examples |
|
|
|
Main Manufacturing Methods |
|
|
|
Large-Molecule APIs include mainly microbial culture APIs and animal cell culture APIs. These APIs are produced by combining techniques such as genetic recombination, cell banking, cell culture, extraction, and purification to generate the active protein components. Examples include antibodies, enzymes, hormones, and interferons. It is expected that they will address unmet medical needs, which were difficult to address with small molecule pharmaceuticals. Since these APIs involve handling biological organisms and proteins, ensuring the sterility of manufacturing facilities and managing the biological aspects of environmental conditions are necessary.
Types and Characteristics of Large-Molecule APIs
Materials Used in Large-Molecule (Biological) Pharmaceuticals and Major Pharmaceuticals
Material | Major Pharmaceuticals | ||
---|---|---|---|
Host Cells | Animal Cells | CHO, SP2/0, NS0, Human Cells (HT1080, HEK), etc. |
|
Microorganisms | E. coli |
|
|
Enzymes |
|
||
Insect Cells |
|
||
Plant Cells | Rice, Tobacco, Carrot |
|
|
Source Cells | Animal |
|
|
Plant |
|
||
Plasma |
|
Microbial Culture APIs
Microbial cultures can be divided into those that use naturally occurring microorganisms and those that use genetically modified microorganisms. The latter involve engineering microorganisms such as E. coli and yeast to incorporate genes that code for the desired substances (APIs) and then producing (expressing) these substances in the microorganisms, followed by purification. Handling genetically modified microorganisms is subject to the Cartagena Protocol on Biosafety. While microorganisms are relatively easy to handle and mass-culture, it is difficult to express the desired substances in an active form. Thus, they are better suited for producing small, simple-structured proteins.
Animal Cell Culture APIs
Similar to microbial culture APIs, animal cell culture APIs utilize recombinant DNA technology. These APIs are produced by expressing therapeutic substances in host animal cells such as CHO cells or COS cells, followed by purification. This method is suitable for producing high-molecular-weight proteins with complex structures, including those with glycosylation. Although animal cells are more challenging to handle and their culture requires advanced control, the resulting substances can closely mimic their natural active forms, including tertiary structures and glycosylation. Compared to microbial cultures, producing a single batch typically takes longer and requires expensive culture media and chromatography resins for purification.
Vaccines
Vaccines are formulations designed to create immunity against pathogens in the body. Their production is restricted to government-designated institutions, and they must pass national inspections before being released. There are broadly two types of vaccines: live vaccines and inactivated vaccines. Inactivated vaccines are safer but less effective than live vaccines, and thus, adjuvants are often added to enhance their efficacy.
Blood Products
Blood products are pharmaceuticals utilizing active components derived from human blood and consist of blood transfusion products and plasma-derived products. Blood transfusion products include whole blood or separated components such as red blood cells, platelets, and plasma. Plasma-derived products are produced by separating and purifying proteins in plasma and include albumin preparations, immunoglobulin preparations, blood clotting factors, and rare disease treatments. The raw blood material is all collected from donations and distributed to three domestic manufacturers via the Japanese Red Cross Society. Except for immunoglobulin, other plasma-derived products have alternatives produced through culturing and other methods, and it is necessary to consider the production efficiency with the balance of raw blood supply and demand for blood products.
Animal-Derived APIs
Animal-derived APIs, excluding those covered under “Animal Cell Culture APIs” and “Blood Products,” are substances difficult to produce using chemical synthesis or genetic engineering. They are mainly extracted and purified from the organs (such as small intestine, pancreas, placenta) of cattle and pigs, with heparin being a well-known example. Ensuring the safety of raw materials is critical for animal-derived APIs, and records of the breeding and slaughtering conditions of the source animals must be well-maintained. Measures against prion diseases such as Bovine Spongiform Encephalopathy (BSE) are particularly important.
Plant-based Pharmaceuticals
These pharmaceuticals utilize chemical components found in plants and include herbal medicines and traditional Chinese medicines, which have been used since ancient times. Well-known examples include the painkiller morphine derived from poppy and aspirin from willow. Traditional Chinese medicines are used in prescribed combinations of multiple herbal medicines (formulations). General manufacturing methods involve selecting parts containing active ingredients, drying, grinding, extracting, concentrating, purifying, and blending various processes.
Large-Molecule (Biopharmaceutical) API Manufacturing Facilities: Key Points for Construction
Planning of Manufacturing Facilities
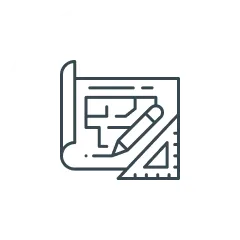
Large-molecule pharmaceutical manufacturing facilities consist of areas for genetic recombination operations and master cell bank construction, culture and purification areas, and formulation areas. Each area must maintain a clean environment to prevent cellular contamination. Facilities should also address the management of personnel gowning, entry and exit, materials handling, and hazardous substances. Within the manufacturing area, equipment such as clean benches, safety cabinets, incubators, centrifuges, cell culture devices, liquid nitrogen storage containers, and sterilization equipment must be installed.
Scale-Up
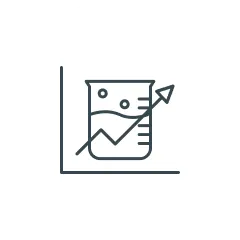
As development progresses from drug discovery to clinical trials and commercialization, the scale-up transitions from beaker to bench (sometimes collectively referred to as kilo lab), to pilot, launch, and finally to commercial scale. Ensuring product quality and production efficiency during this scaling process is vital. Scale-ups from laboratory scale to production scale are not solved by merely increasing the volume or time in reactors. Although there are basic approaches to parameter setting and calculation formulas, expected yields often are not achieved. Therefore, trial and error in scale-up experiments (process development) is necessary. While this is common for both small molecule APIs produced by chemical synthesis and large-molecule APIs involving cell cultures, it is more delicate with the latter. After evaluations in pilot plants, equipment for commercial production is constructed, and it must adequately reflect requirements from process development.
Operational Schedule
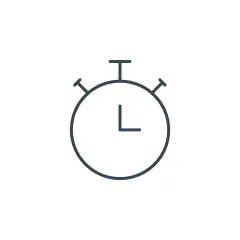
For cultured APIs, the manufacturing process is broadly divided into culture (upstream) and purification (downstream) processes. The culture process operates for several days to about a month in a single device (bioreactor), while the purification process typically operates each device for one day. To increase operational efficiency and avoid excessive design specifications, the culture process usually involves multiple systems for each purification system. Optimal equipment design and operation require an operational schedule that includes times for C/SIP and column regeneration and equilibration.
C/SIP
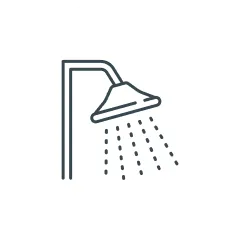
Cleaning-In-Place (CIP) and Sterilization-In-Place (SIP) systems clean and sterilize manufacturing equipment without disassembly or relocation. CIP uses water or cleaning solutions containing acids, bases, or surfactants to clean the interior surfaces of equipment and pipes. It is essential that cleaning solutions and rinse water are sprayed on all surfaces and residues are removed using spray balls. Internal pipe cleaning ensures maintained cleaning performance by securing flow rates and eliminating dead spaces. SIP sterilizes equipment interiors and pipes by heating the system using saturated steam (pure steam) derived from purified water. Although C/SIP offers reproducible cleaning and sterilization compared to equipment disassembly, it complicates the system and increases initial costs.
Single-Use Technology
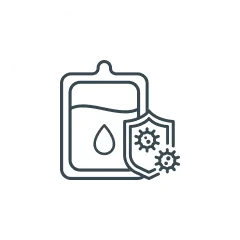
Due to the high requirements for cleanliness and sterilization in biopharmaceuticals and vaccines, single-use technology, which avoids the need for cleaning and sterilization, is effective for early-stage production and multi-product manufacturing. Single-use technology, ranging from simple mixing equipment to culture devices and stirrers, is widely available. Single-use parts, such as those for culture, purification, medium adjustment, pH adjustment, inactivation, filtration, and connectors, can be combined for fully automated processes. However, larger storage spaces are required. A thorough risk assessment of the sterility, extractability, integrity, and inter-process connection methods of single-use equipment must be conducted. Nevertheless, it simplifies and makes the construction of production equipment more flexible by omitting cleaning and sterilization-related equipment.
Continuous Production
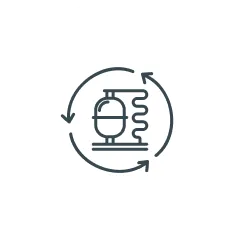
Continuous production of biological APIs involves continuous culture (perfusion culture) with ongoing medium feeding and harvest of culture fluid, along with continuous purification using multiple small-scale columns performing loading, washing, and recovering simultaneously. Continuous production promises reduced development time due to the elimination of scale-up, equipment miniaturization, and reduced facility space. Regulatory bodies such as the ICH and others are promoting its adoption. However, compared to batch production, considerations for control strategies (State of Control) and lot definition are necessary.
Strengths of CM Plus
①Engineering + CM Method
The CM method is a project management system that integrates the client’s perspective with designers to operate and manage projects transparently, ensuring success from the aspects of QCD (Quality, Cost, Delivery) + EHS (Environment, Health, Safety). Professionals, including Construction Managers (CMr) who specialize in management, work on behalf of the client.
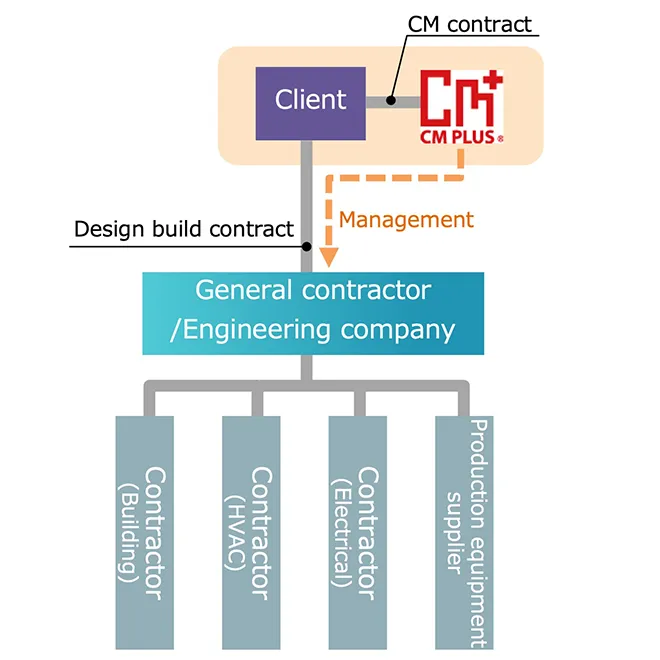
At CM Plus, we conduct engineering (design) in-house. We have engineers who are well-versed in manufacturing processes, equipment and facilities, construction, and manufacturing support facilities (such as electrical systems, HVAC, and utilities). This allows us to oversee the entire facility from the initial planning stages, enabling the construction of integrated and cohesive layout facilities.
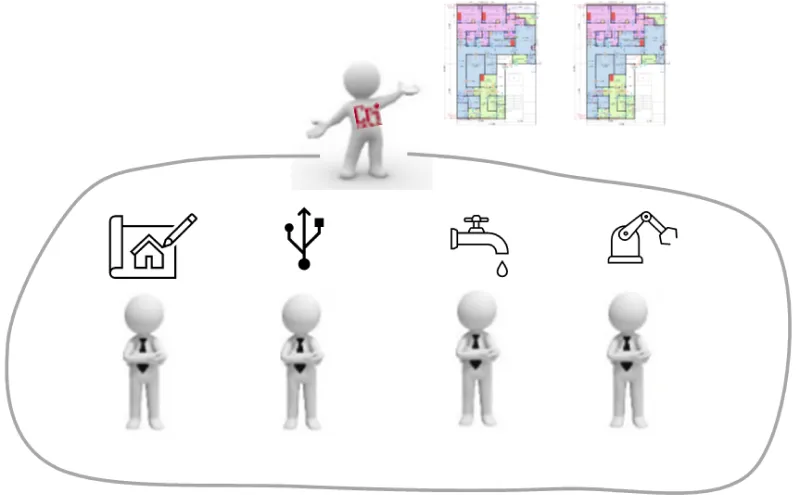
②Comprehensive Coordination of Production Equipment and Building Facilities
With a focus on designing from the production process perspective, we execute designs that start from the internal aspects like building production equipment lines, layouts, and internal flow/logistics, leading to the creation of API (Active Pharmaceutical Ingredient) factories that are in harmony with the production system. Our planning extends to the intangible aspects of the production system as well.
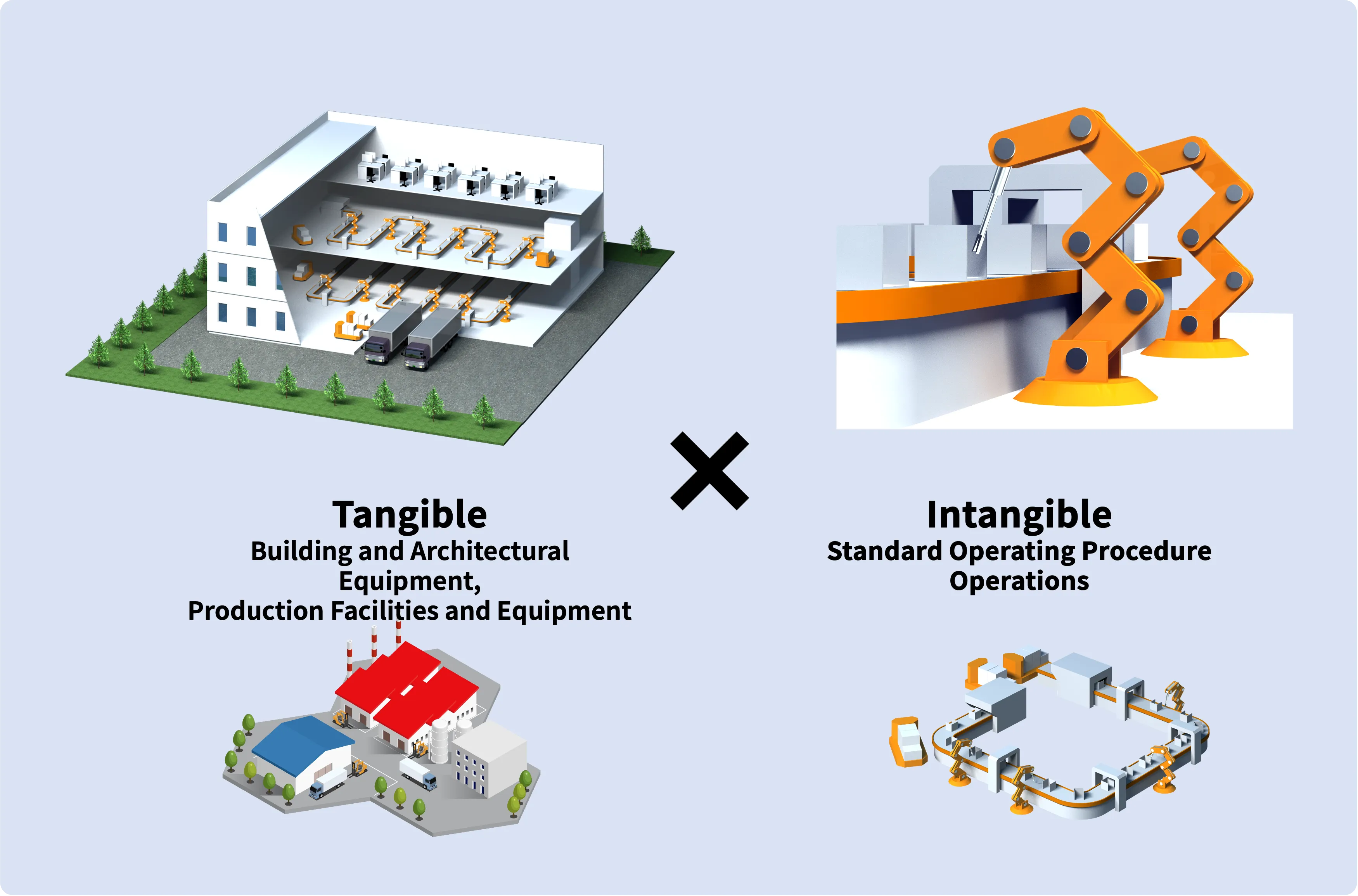
Our team consists of project managers and professional engineers experienced in factory construction across various fields. This allows us to manage the overall project schedule comprehensively, including not only the building and production support facilities but also providing support for the procurement, production management, and coordination of delivery plans of production equipment.
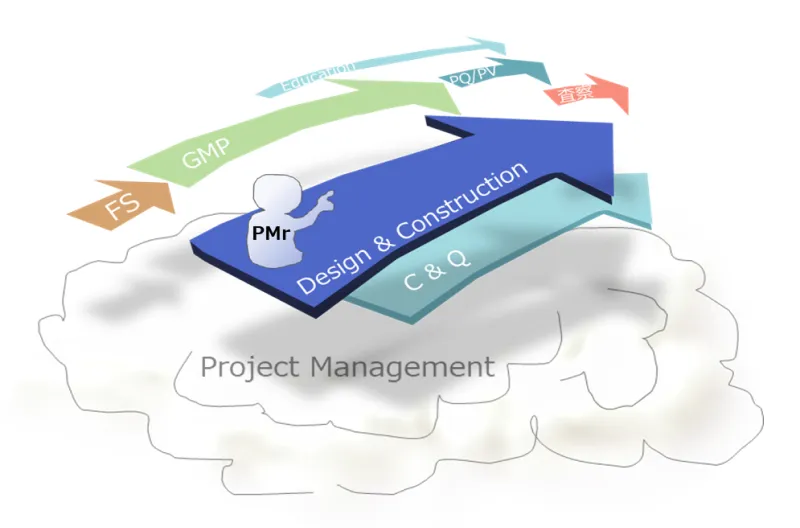
Services provided by CM Plus
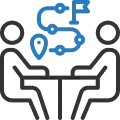
Business Concept
At the early stages of your business and investment planning, we conduct surveys on the current status of production and logistics facilities, identify areas for improvement, explore future concepts, and optimize equipment. We calculate investment costs, examine cost-effectiveness, consider BCP (Business Continuity Planning), and SDGs (Sustainable Development Goals) compliance—all tailored to meet your needs. We also create basic concepts for production and logistics facilities, including process flow diagrams, mechanical flow diagrams, material balances, basic layouts, major equipment lists, automation plans, energy-saving plans, facility operation plans, and staffing plans, thereby visualizing the investment image.
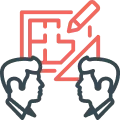
Basic Planning
In basic planning (conceptual design), we understand the contents of the business and investment plans, analyze and organize facility requirements, and document them as a User Requirements Brief (URB). Based on the URB contents, we also calculate the project’s estimated costs and consider an overall project execution plan, all tailored to meet customer needs.
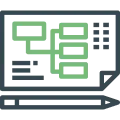
Basic Design
During the basic design phase, we finalize the URB details, consider the necessary facilities and equipment, and compile specifications and arrangements for production and logistics equipment, buildings, and utilities. Specifically, for process design, we create PFDs (Process Flow Diagrams), P&IDs (Piping and Instrumentation Diagrams), datasheets, time schedules (OTS), equipment specifications, and other basic design documents. We also organize regulatory standards, governmental applications, and environmental conditions related to facility design and construction, support setting the project master schedule and overall execution plan, and prepare and support preliminary coordination with relevant authorities, power, and utility suppliers.
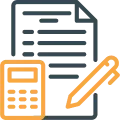
Quotation Inquiry
During the stage of selecting equipment manufacturers and construction companies, we support confirming the optimal construction project execution system by examining order divisions and considering separate or lump-sum orders according to the project’s overall execution plan. We also conduct selection of quotation destinations, creation of inquiry documents, and evaluation and consideration of quotes—as per customer requirements.

Detailed Design and Manufacturing Management
In the detailed design and manufacturing phase, we oversee the design management to ensure that design offices, construction companies, and equipment manufacturers reflect the URB, basic design documents, and related regulatory standards in their designs and are progressing according to schedule.
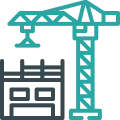
Construction and Installation Phase
During the equipment manufacturing and construction execution phases, we oversee to ensure that equipment manufacturers and construction companies reflect the URB, basic design documents, and related regulatory standards in their manufacturing and construction activities. In the case of CM (Construction Management) work, we also confirm the overall schedule’s progress, manage the coordination between equipment manufacturers and construction contractors, and control the overall project costs—tailored to customer requirements.
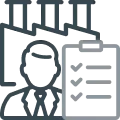
Commissioning
To achieve high-quality and efficient qualification execution, we support creating validation master plans and risk assessments from the planning stage. We prepare protocols for executing qualifications (DQ, IQ, OQ, PQ) and provide services that support execution stages to meet customer needs, thereby reducing their burden.
Facility Operation
Related Projects
Useful Information
Please refer to the articles related to active pharmaceutical ingredients on our information dissemination site, “GMP Platform”.
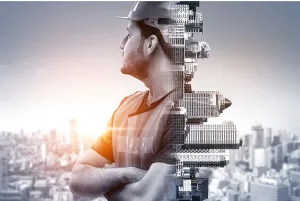
“How to Build a Pharmaceutical Factory: Special Edition”
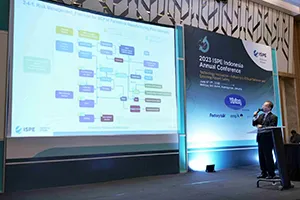