Basic Design in Factory Construction
In the basic design phase, we review and propose solutions to realize the concepts established during the basic planning (conceptual design). We then solidify the detailed specifications and create the blueprints. Considering the investment costs and future plans, we finalize the specifications that meet the client’s requirements and create the drawings.
As the final step in the basic design process, we conduct a preliminary estimate based on the basic design. After confirming that the selected specifications during the basic design phase fall within the client’s budget, we proceed to the next step of “Procurement.”
Implementation Items of Basic Design
Documents Created in Basic Design
Based on the basic planning (conceptual design), we create more detailed design documents for production equipment, architecture, HVAC systems, plumbing and sanitation facilities, utility facilities, and electrical installations.
These design documents are also used as specification requirements for suppliers.
Example Table of “Deliverables Content”
General Design |
|
---|---|
Architecture |
|
HVAC Equipment |
|
Plumbing, Utility, and Fire Protection Equipment |
|
Electrical Equipment |
|
Preliminary Cost Estimate in Basic Design
We calculate a preliminary estimate based on the basic design. This estimate is more accurate than the one made during the basic planning (conceptual design) phase, and it serves as a final confirmation against the project budget.
Differences Between Basic Design and Detailed Design
The basic design aims to finalize specifications and quantities that will impact production capacity, product quality, costs, and schedules in preparation for project execution.
In contrast, the detailed design involves finalizing all the detailed information necessary for manufacturing and construction.
At CM Plus…
Clear Deliverables and Goals in Basic Design
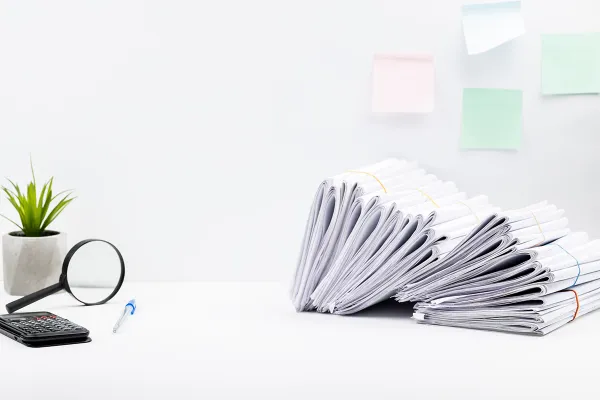
The design documents we create are customized and clarified based on our company’s standard deliverable list, tailored to the project’s and client’s needs. The design documents and URS (User Requirement Specifications) produced in the basic design phase are necessary for subsequent steps such as contractor quotation requests, detailed design, and commissioning activities.
Furthermore, any issues or review items that arise during the basic design process are listed, and by the end of the basic design phase, we ensure that these issues are resolved.
For factories dealing with pharmaceuticals, medical devices, etc., we can add a validation master plan (VMP) for the project to the basic design deliverables upon request.
- URS: User Requirement Specification
Furthermore, in Pharmaceutical Factories…Traceable URS for Qualification
Through pre-system classification, we identify direct impact systems and create their URS. To be utilized in QRM, the URS clearly lists CQAs, CPPs, and GMP requirements, serving as the criteria for design review and design qualification after the detailed design phase. We conduct a GMP compliance evaluation for the basic design document package, including the URS, and document and ensure that all GMP requirements are reflected in the basic design documents.
- Direct Impact System: Systems expected to have a direct impact on the product quality of pharmaceuticals and subject to qualification.
- QRM: Quality Risk Management
- CQAs: Critical Quality Attributes
- CPPs: Critical Process Parameters
- GMP: Good Manufacturing Practice
-
Please refer to this for explanations on UR and URS.
-
Please refer to this for information on qualification and validation activities.
Discovering Optimal Specifications and Functions for Clients
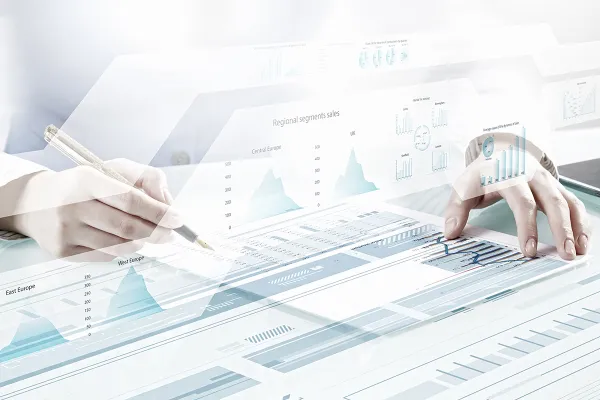
To materialize user requirements (UR), we propose the most suitable technologies based on trends and track records, while investigating the advantages and risks of the latest technologies. We also evaluate and decide on the adoption plan from various perspectives such as productivity, future potential, energy and labor savings, running cost reductions, operability, maintenance, and installation costs.
As professionals in technology and project management, CM Plus collaborates with clients from a fair standpoint, pursuing specifications that satisfy all project stakeholders.
-
Please refer to this for information on energy-saving, carbon neutrality, BIM, DX, etc.
Centralized Management by the Project Manager
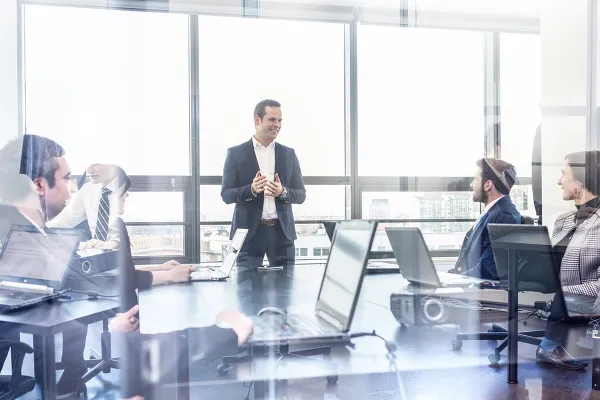
There are numerous items to be examined and finalized in the basic design phase, such as production equipment, manufacturing management systems, logistics systems, architecture, facility ancillary equipment, and commissioning activities. This is the most crucial period for ensuring the success of the project, yet it is often the time when the least amount of time can be allocated.
At CM Plus, experienced project managers well-versed in all these aspects will schedule and guide the process to ensure that the client’s requirements are designed within the stipulated timeframe.
Cost Management
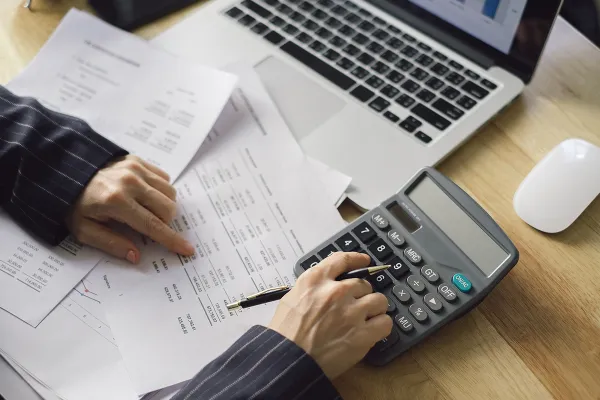
Based on the determinations made during the basic design phase, we provide an approximate estimate. This includes not only buildings and their ancillary facilities but also pharmaceutical machinery, manufacturing management systems, and logistics systems, offering a total project cost estimate.
Upon reaching an agreement with the client on the total cost, we proceed to the next step—calling for procurement (supplier selection).
See other phases
Related Contents
Useful Information
Please also refer to the articles on our information dissemination site, “GMP Platform.” Although the title contains “Pharmaceutical Factory Construction,” the content is applicable to the construction of factories in various industries, not limited to pharmaceutical factories.
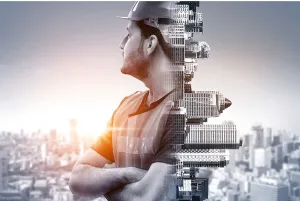
“How to Build a Pharmaceutical Plant”
Integrating know-how for the success of pharmaceutical factory construction projects. It provides detailed explanations and key points for each step, from overall project planning (= creating the project framework) to basic planning and basic design.
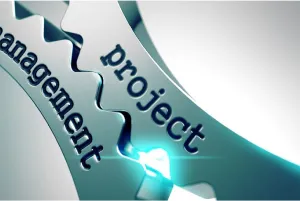
“Owner’s Project Management in Pharmaceutical Facility Construction 2nd Edition”
The 7th installment in the series on owner’s construction project management. What is basic design?