Validation in Pharmaceutical Manufacturing
Validation is defined as the following;
“A documented program that provides a high degree of assurance that a specific process, method, or system will consistently produce a result meeting pre-determined acceptance criteria. (ICH Q7A)”
“Establishing documented evidence which provides a high degree of a high degree of assurance that a specific process will consistently produce a product meeting its predetermined specifications and quality attributes.(FDA Process Validation Guidance 1987)”
High-quality and efficient validation execution is one of the most important challenges to be achieved in new construction or renovation projects of pharmaceutical factories. Recently, the pharmaceutical industry has been transitioning from traditional validation to “science and risk-based validation.” This transition requires the implementation of risk assessments and the creation of validation plans based on these assessments, increasing the effort required for validation.
CM Plus offers services tailored to customer needs, ranging from support for creating validation master plans and risk assessments, to preparing and executing protocols for qualifications (DQ, IQ, OQ, PQ) from the planning stage. This helps reduce the burden on customers.
Additionally, we can accommodate requests for validation tasks alone, separate from planning and design tasks. We are flexible in responding to customers who are already in the construction phase, so please feel free to consult us.
Feel free to contact us regarding validation.
The Flow of Validation in a Project
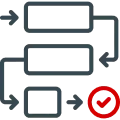
Preparing the Validation Master Plan
The Validation Master Plan (VMP) is a comprehensive validation plan compiled for a pharmaceutical plant construction project. It typically documents the following items, tailored to the project content:
- Validation policy
- Organizational structure for validation activities
- Systems subject to validation (facility, equipment, machinery, etc.)
- Overview of manufacturing processes
- Formats for various protocols and reports
- Validation schedule
- Change control and deviation management
- References to documents, etc.
The VMP is summarized during the basic planning stage of the overall project schedule, clarifying the validation policy for the project.
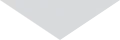
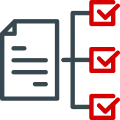
Conducting Risk Assessment
In recent years, the approach of quality risk management has been integrated into the planning process for validation. A validation plan is created based on the results of the risk assessment. During the risk assessment phase, the system range subject to qualification is determined, and the content of verification items to be executed during DQ, IQ, OQ, and PQ is planned.
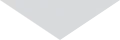
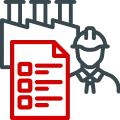
Executing Qualification (DQ, IQ, OQ)
Based on the results of the risk assessment, protocols according to various qualification plans are created. During the qualification execution period, it is crucial to manage changes and deviations properly, ensuring qualifications are conducted following approved design documents and protocols. Recently, it has become common practice to reference the results of Factory Acceptance Tests (FAT) or Site Acceptance Tests (SAT) conducted by suppliers in the IQ and OQ qualifications to conduct qualifications.
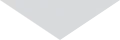
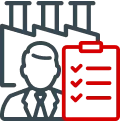
Executing PQ, Process Validation, Cleaning Validation, and Analytical Method Validation
After completing IOQ, PQ and process validation (PV) for the products to be manufactured are conducted. PQ uses raw materials or placebos used in actual manufacturing to verify manufacturing under worst-case operating conditions, sampling crucial processes and intermediates to ensure manufacturing is feasible within the expected operating range. Given that expensive raw materials may be used for PQ and PV, it is important to utilize OQ data, carefully scrutinize PQ and PV execution items to create efficient validation plans, and execute them rationally. Moreover, for process validation, validation of cleaning methods and analytical methods for evaluation is also necessary. Production can only start once all these validations are complete.
At CM Plus…
Determining Qualification Scope Using Risk-Based Approach
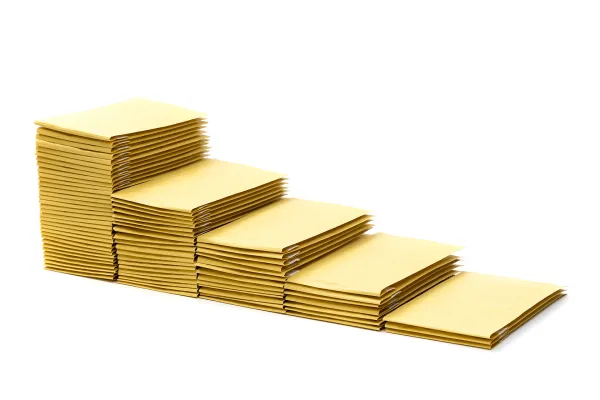
At the planning stage of validation, a risk assessment is first conducted to evaluate whether the facilities and equipment (systems) being introduced directly impact product quality and patient safety. Based on this evaluation, the scope of systems subject to qualification is determined (system assessment). Conducting an accurate system assessment enables rational qualifications, leading to improved validation work quality and reduced unnecessary costs.
Drafting Qualification Plans Based on URS
Annex 15 of the PIC/S GMP specifies that the user requirement specification (URS) should be referenced throughout the validation lifecycle. Hence, URS needs to be referred to from the initial stages of qualification. At CM Plus, we propose drafting qualification plans starting with the URS. This approach ensures that the requirements specified in the URS are directly linked to the verification items, making the relationship between the requirements and the qualification clear and enabling the creation of appropriate qualification plans. Furthermore, even during post-implementation operations, referencing the URS facilitates proper change management.
Validation for Computer Systems/Software
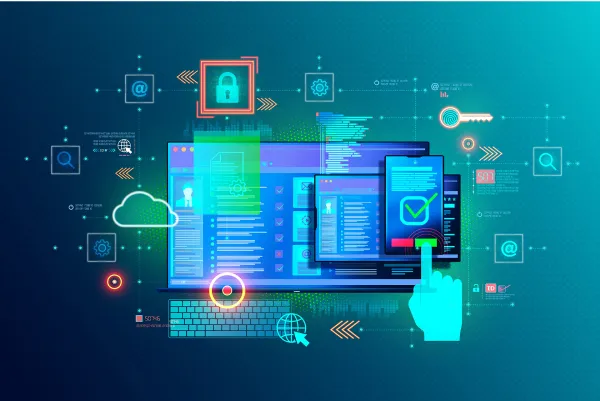
We also provide support for implementing computerized system validation (CSV) and computer software assurance (CSA) for the introduction of IT systems like Manufacturing Execution Systems (MES) and Laboratory Information Management Systems (LIMS). Our approach is in compliance with ISPE GAMP5 (2nd Edition) and the FDA’s CSA draft guidance, providing risk-based plan creation and test activity proposals. We also offer advice on data integrity requirements (security, audit trails, data storage, etc.) necessary for computer systems.
Document Management Based on Good Document Practice (GDP)
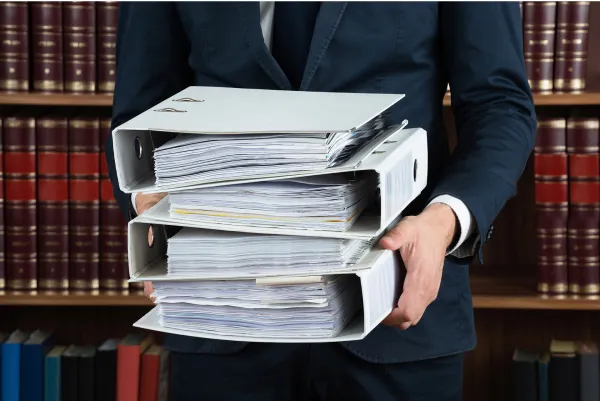
Successful validation cannot occur without successful document management within a project. At CM Plus, we provide guidance and support based on Good Document Practice (GDP), including supplier document management and the formalization of record creation rules, to support the creation of GMP-compliant documents. Additionally, we support the creation of GMP educational materials, PQ/PV protocols, and SOPs based on customer needs.
-
For validation of manufacturing facilities and architectural equipment,
please refer to Commissioning & Qualification (C&Q) in engineering services.
Related Contents
Useful Information
Please refer to the articles on our information dissemination site “GMP Platform.”
Though the title includes “Pharmaceutical Plant Construction,” the content applies to construction in various industries, not limited to pharmaceutical plants.
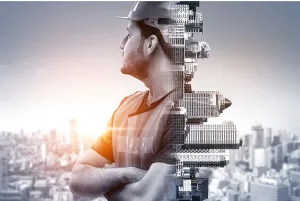
“How to Build a Pharmaceutical Plant”
The know-how for successfully completing pharmaceutical plant construction projects is compiled. It covers the C&Q/Validation activities that should be performed at each stage of the project. It explains everything from C&Q strategy formulation to DR/DQ, SAT, and IQ/OQ.
We have published a book in English. Please refer to this news.
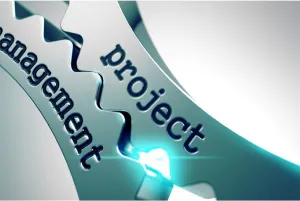
“Owner’s Project Management in Pharmaceutical Plant Construction 2nd Edition”
The 16th installment in a series about the owner’s construction project management, focusing on qualification.